When it comes to Electrical, Electronic, and Environmental (EEE) inspections, ensuring safety and compliance is a crucial part of protecting both employees and the environment. An EEE inspection helps identify hazards, ensures adherence to regulations, and enhances workplace safety. However, there are common mistakes that often occur during these inspections, which can compromise the effectiveness of the process and potentially lead to costly errors or risks EEE inspection.
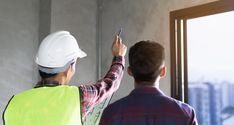
To help you navigate an EEE inspection with ease and avoid common pitfalls, here’s a list of the Top 5 Mistakes to Avoid:
1. Skipping a Detailed Pre-Inspection Checklist
One of the biggest mistakes in preparing for an EEE inspection is not having a comprehensive pre-inspection checklist. Failing to conduct a thorough assessment of all relevant components—such as electrical systems, environmental regulations, and equipment performance—can lead to missed issues during the actual inspection.
Solution: Create a detailed checklist that outlines all the necessary inspections for electrical wiring, environmental impact assessments, and electronic equipment compliance. Review it before the inspection day to ensure nothing is overlooked.
2. Not Involving the Right Team Members
EEE inspections require a multi-disciplinary approach. Often, one person or team is assigned the responsibility of conducting the inspection, but they may lack the expertise in certain areas—such as electrical safety, electronic waste disposal, or environmental impact assessments.
Solution: Assemble a diverse team that includes experts in various areas. This might include electrical engineers, environmental consultants, and safety officers. By involving the right professionals, you ensure that each inspection aspect is thoroughly examined.
3. Ignoring Documentation and Records
Another common mistake is not having the proper documentation or records on hand. Inspections require detailed records for past compliance checks, maintenance logs, and equipment certifications. If these are missing or incomplete, it becomes difficult to assess whether previous issues have been addressed or if the equipment meets current regulations.
Solution: Ensure that all necessary documents are readily available and up to date. This includes maintenance schedules, safety inspection reports, equipment manuals, and certification records. Keep these files organized for easy access during inspections.
4. Failing to Address Minor Issues That Could Lead to Bigger Problems
During an EEE inspection, minor issues are often overlooked in the rush to check off the more significant items. These smaller problems, if left unchecked, could evolve into more serious hazards in the future. For instance, loose wiring, improperly stored hazardous materials, or outdated equipment can lead to potential failures or accidents.
Solution: Pay attention to both major and minor issues. Even if a problem seems trivial, it’s important to address it immediately to prevent it from becoming a bigger issue down the line. Regular, proactive inspections can help keep operations running smoothly and reduce long-term risks.
5. Not Keeping Up with Changing Regulations and Standards
EEE regulations and standards are constantly evolving, making it difficult to stay updated on the latest compliance requirements. Failing to keep track of these changes can lead to unintentional violations, which may result in fines, penalties, or operational shutdowns.
Solution: Stay informed about current regulations by subscribing to industry newsletters, attending training, and consulting with experts. Regularly review industry standards to ensure that your processes align with the latest safety, environmental, and electrical requirements.
Conclusion
EEE inspections are an essential part of maintaining safety, ensuring compliance, and promoting efficiency within your organization. By avoiding these five common mistakes, you can ensure a smoother inspection process, improve workplace safety, and prevent costly errors. Always remember, preparation and attention to detail are key to a successful inspection.
4o mini